Prototype and Production Tooling for injection moulding with minimal lead time to enable functional testing and produce high precision plastic components.
Soft & Production Tooling
Technical Features
Soft Tooling
Materials: Made from softer, less durable materials like aluminum, silicone, or composite resins.
Process: Often created via CNC machining, 3D printing, or low-cost molds.
Lifespan: Suitable for low to medium volumes (e.g., 100–10,000 parts).
Precision: Moderate tolerances, ideal for prototyping or short runs.
Production Tooling
Materials: Built from hardened steel or high-grade alloys for durability.
Process: Precision-machined using advanced techniques like EDM (electrical discharge machining).
Lifespan: Designed for high-volume production (e.g., 100,000+ parts).
Precision: Tight tolerances and superior surface finishes.
Applications
Soft Tooling
Prototyping: Rapid iteration of product designs.
Bridge Tooling: Short-run production before final tooling.
Low-Volume Manufacturing: Custom parts, niche markets, or pilot batches.
Industries: Consumer goods, medical devices, automotive prototypes.
Production Tooling
Mass Production: High-volume manufacturing of standardized parts.
End-Use Parts: Automotive components, electronics housings, packaging.
Industries: Automotive, aerospace, appliances, and consumer electronics.
Advantages
Soft Tooling
Lower Cost: Cheaper materials and faster fabrication.
Faster Lead Time: Days/weeks vs. months for steel tools.
Flexibility: Easy to modify for design changes.
Ideal for Testing: Validates designs before investing in hard tooling.
Production Tooling
Durability: Withstands millions of cycles without wear.
Cost-Efficiency: Lower per-unit cost for large volumes.
High Precision: Consistent quality for critical applications.
Surface Finish: Polished molds enable smooth, aesthetic parts.
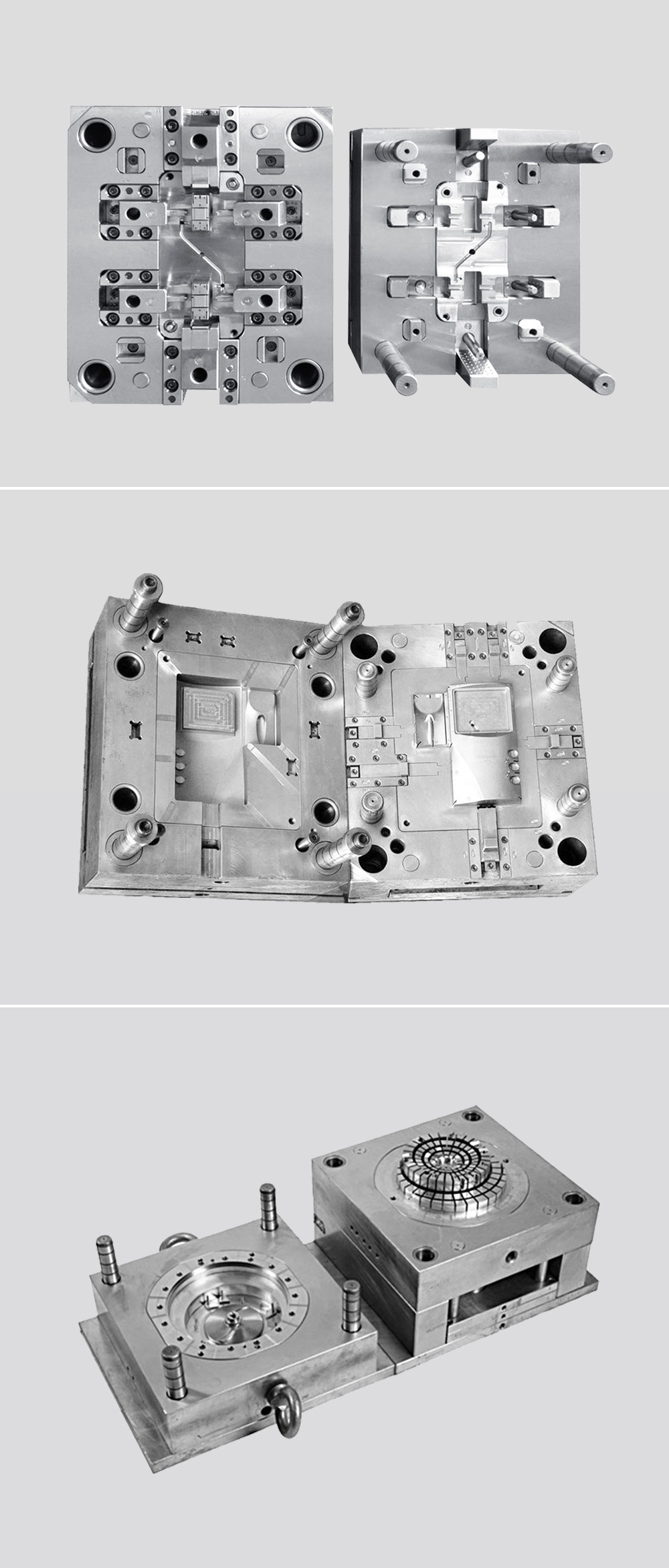