Factory Free sample Plating - RIM – Protom Detail:
RIM
Trusted for high quality rapid injection molding (RIM) services, our company offers solutions which demonstrate all the advantages of RIM technology such as thermal insulation, heat resistance, dimensional stability and a high level of dynamic properties.
Major advantages
· Reduced tooling costs
· Freedom of design
· Higher strength to weight ratio
· Eliminated secondary operations
Parts produced through RIM process are dimensionally stable, wear resistant and chemical resistant. For larger plastic parts manufactured in low to mid volumes RIM is an outstanding choice.
Plastics used in RIM process are thermosets, either polyurethane or foamed polyurethanes. Mixing of the polyurethane is done in the tool cavity. Low injection pressures and low viscosity mean that large, complex parts can be produced in a cost-efficient manner.
Energy, floor space as well as equipment used in RIM process for making the same product is considerably low, making it a viable option low and mid volume production runs. The process is more automated as well, compared to alternatives. Get in touch today for more information on RIM process.
Product detail pictures:
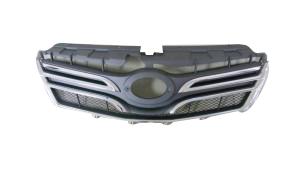


Related Product Guide:
Cooperation
We pursue the administration tenet of "Quality is remarkable, Services is supreme, Status is first", and will sincerely create and share success with all customers for Factory Free sample Plating - RIM – Protom, The product will supply to all over the world, such as: Jamaica , Morocco , Georgia , We are seeking the chances to meet all the friends from both at home and abroad for the win-win cooperation. We sincerely hope to have long-term cooperation with all of you on the bases of mutual benefit and common development.

The company has a good reputation in this industry, and finally it tured out that choose them is a good choice.
